Pressure and robots powered the cleaning of OL3’s steam generators
Even though this annual outage was the first for the Olkiluoto 3 plant unit, previous experience on washing its steam generators was available. They were, after all, already cleaned once during the test operation stage. The same job has now been completed even after an operating cycle. The annual outage for OL3 continues, but regarding steam generator cleanings, the task is now completed.
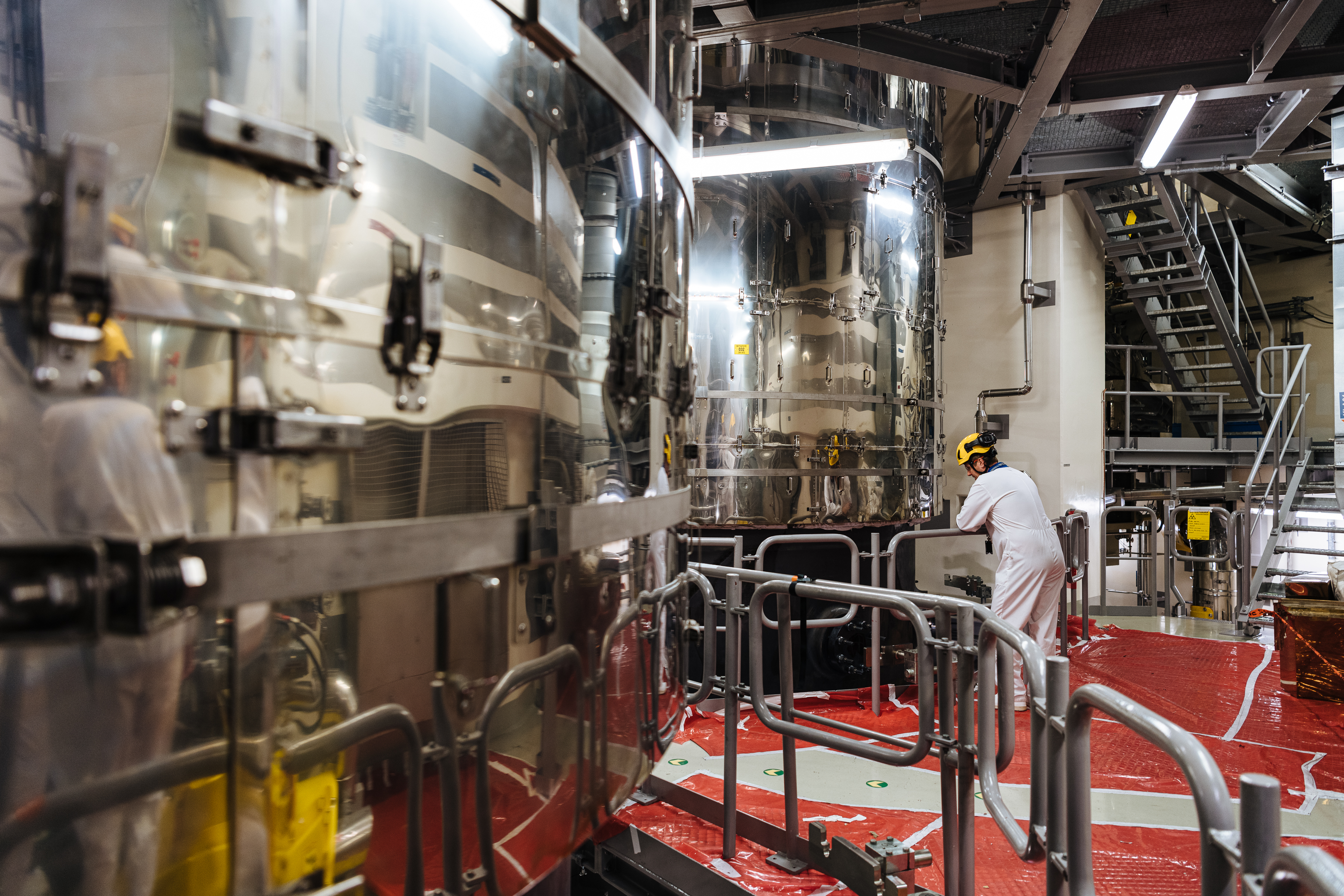
Washing the steam generator tubes is an important procedure. The tubes must be regularly cleaned, since feedwater flow causes impurities to accumulate at their roots which would wear down the tubes over time. The worst possible scenario would be leakage through a thinned tube wall. For this year, the surfaces have now been cleaned and their condition has been inspected.
- We started the washing on Wednesday 13 March, and everything was done by Easter. We were able to keep to the schedule quite well, says Jussi Kylliäinen who was responsible for the worksite related to the washing of the steam generators.
Approximately thirty workers were reserved for the washing operation; most of them were German, and the official language of the worksite was English. Even though the plant unit is new, some experience is available for similar washing operations; for most participants, however, this was the first time.
Quite a few tubes to clean
The large size of the OL3 plant unit can also be seen in the steam generators and, of course, the substantial scope of the washing operation. This was especially true since all four steam generators at the plant were washed.
- One steam generator has a diameter of four metres and a total height of 23 metres, and each individual steam generator contains approximately 6,000 finger-width tubes, Jussi Kylliäinen explains.
The washing was mainly performed by robots and no chemicals were used in the cleaning. The cleaning medium is demineralised water which is propelled at a pressure of 200 bar.
- This corresponds to the pressure in a normal pressure washer, he says.
Between 24 and 28 hours were reserved for washing one steam generator; however, some time had to be allocated for preparatory work and the mechanical drying that was started after the wash.
- Drying always took 10 hours after the washing, since the visual inspection performed with cameras would not have been doable in the presence of moisture. It would have literally fogged up our lenses, Mr Kylliäinen explains.
The visual inspection both ensures that the surfaces are clean and verifies that no foreign material remains in the steam generator.
Good cooperation from day one
For Mr Kylliäinen, the annual outage work for OL3 is now complete.
- I can now say that I feel good, but the job was quite challenging, especially since I joined this major project in the middle of the outage, he says.
Even though the days were occasionally long and some challenges were encountered, Mr Kylliäinen is happy with the end result.
He points out, however, that this was helped by the team of professionals and, in particular, its German supervisor Oliver Birthelmer. They had good cooperation right from the start.
- Every aspect of our cooperation with Framatome was excellent, from start to finish – and I also received great support and assistance from my own colleagues.
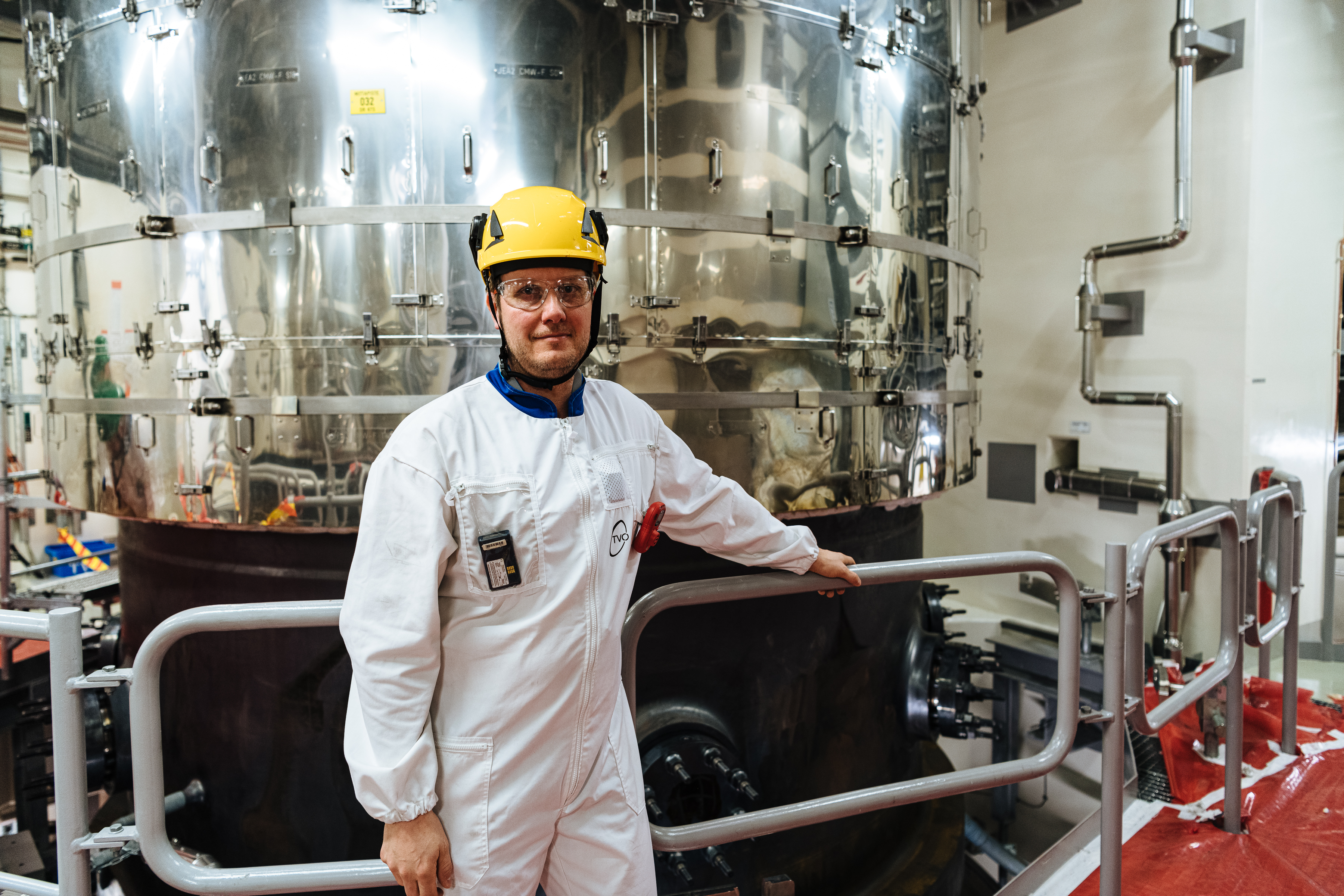
A veteran of Olkiluoto
Even though the project was new for Mr Kylliäinen, he is very familiar with Olkiluoto and the OL3 plant unit in particular.
- I first walked in through the main gate in 2006 and immediately joined the OL3 project. I’ve been on the island ever since, he explains.
His employer did change, however, since Mr Kylliäinen spent his first 11 years working for the plant supplier Areva. He has now worked for TVO for four years.
- When I arrived, I didn’t see myself working on the first annual outage as well – but time passes quickly.
Text: Ville Kulmala
Photos: Tapani Karjanlahti
Share